The electric vehicle controller belongs to the core part of the electronic control device. It is used to control the start, operation, forward and back, speed, stop and other electronic devices of the electric vehicle motor. It likes the brain of the electric vehicle,which is still an important part .
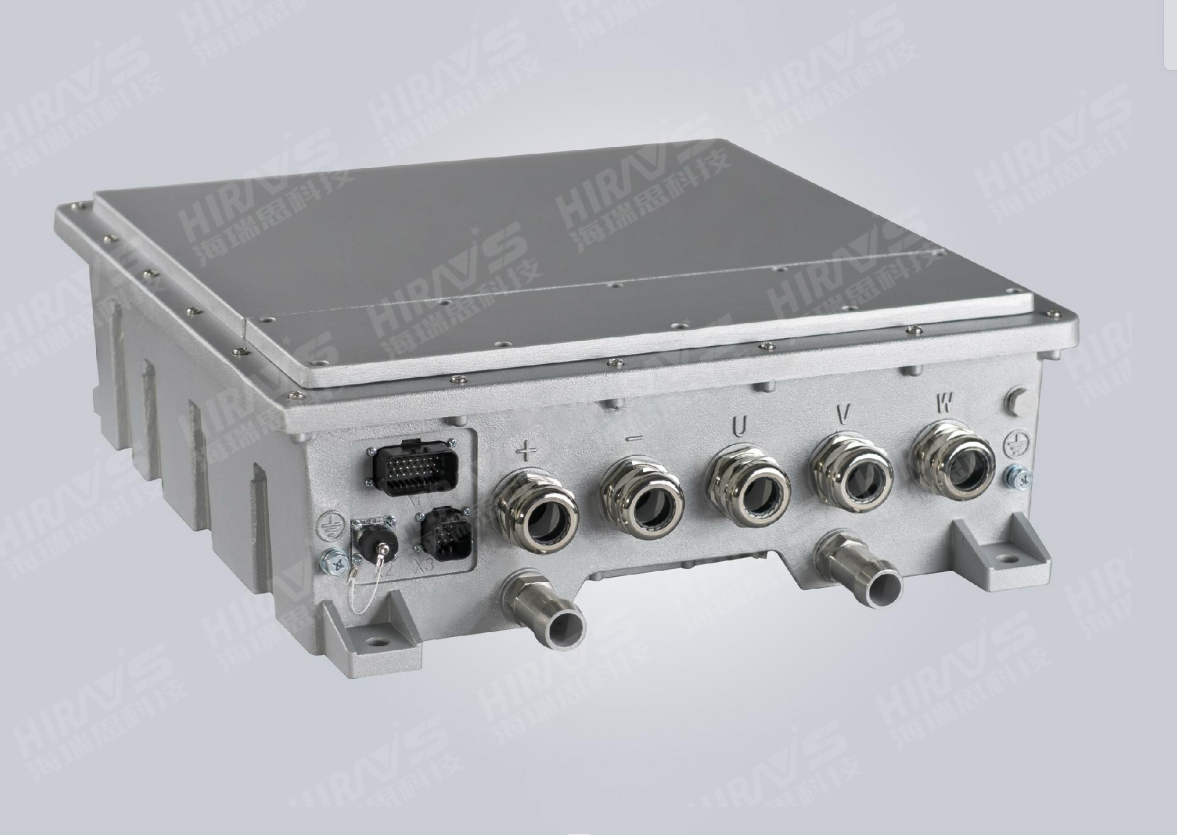
It is easy to encounter rain and snow when driving. In order to ensure safe driving, the controller must be able to prevent dust and water.
So how can we test the waterproof performance of the controller, that is, the air leakage?
Parts to be tested for air leak test:
Parts to be tested of controller die-casting shell: water-cooled pipe shell (semi-finished product test) Test pressure: 30KPa / 200-300kpa.
Parts to be tested for the finished product of the controller: after the shell is assembled, the test pressure at the joint and shell (semi-finished product test) Test pressure:10-15kpa.
Air leak test system = instrument + tooling (optional) + mold (optional)
Controller die-casting shell's air leak test equipment: high-precision differential pressure instrument + floor-standing 3T pressure tooling + custom sealing mold.
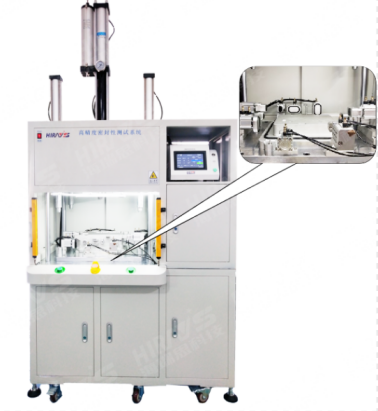
Controller finished product leak test equipment: high-precision differential pressure instrument + quick connector.
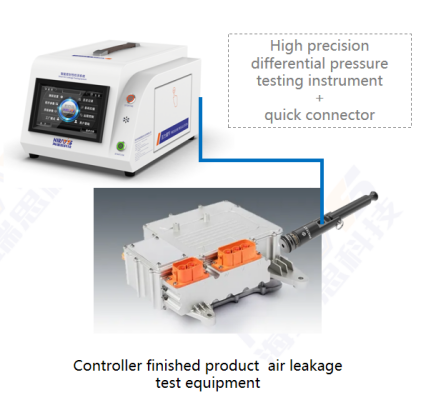
Problems that may be encountered in the process of leak testing:
Problem 1: In the production process of die-casting shell, it is necessary to detect the leakage caused by machining defects and the detect the tightness of water-cooling pipeline and shell at the same time. The detection is often carried out in two steps, and the detection efficiency is very low;
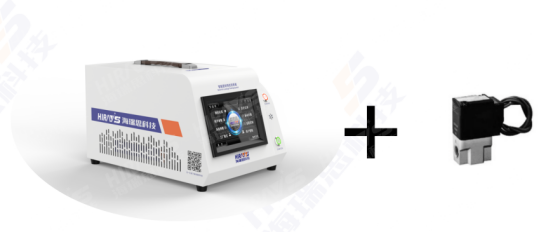
Solution: Using Hirays’ high and low pressure instrument + leak free 3-way valve, can realize the water-cooling pipeline and shell be tested in one machine, reducing the handling time and manpower waste;
Problem 2: Because there are so many connector holes reserved in the die-casting shell ,the positions need to be blocked during detection, and it needs to be blocked on 3, 4, or even 5 sides; once the mold design is unreasonable , without much consideration, it will cause the tightness to be unstable, and eventually lead to inaccurate test results;
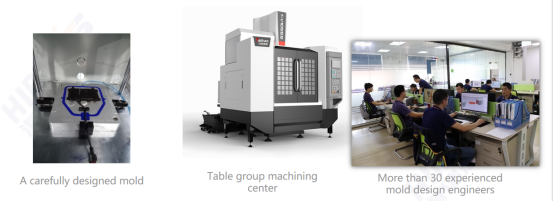
Solution: Hirays has more than 30 experienced mold design engineers and 8 high-precision CNC machining centers; The machining accuracy can reach 0.02 mm;
Reasons for choosing us
Program Advantages:
l High precision mold processing , up to 0.02mm;
l Air tightness detector, resolution up to 0.1PA;
l Hirays allows your controller to be tested in one testing equipment;
l Hirays has more than 30 mold design engineers and a strict evaluation system;
l The designed detection system strictly considers the stability and accuracy of the test results;
Program benefits:
A. High precision, ensuring the stability of the mold;
B. High resolution, even the smallest leakage can be accurately detected ;
C. One set of equipment completes the controller's water-cooling pipeline and shell testing, saving at least 15 minutes of man-hours each time;
D. Experienced engineers bring sophisticated mold design, so that each mold you use is stable and reliable ;
E. Strict requirements, bring a stable detection system to help you select defective products ;
Cooperative customers
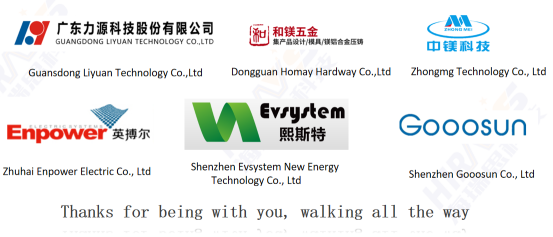